The Digital Future of Process Chemistry and Technology – Learnings from The Royal Society of Chemistry Meeting
In November I attended The Royal Society of Chemistry (RSC) meeting – The Digital Future of Process Chemistry and Technology interest group meeting, hosted at the RSC’s office at Burlington House, London.
In this blog I share my findings, takeaways and opinions. Digital tools are here. How do we make the most of them? How do we empower and train people to use them? !
Workforce Skill Sets
The morning session encapsulated discussions around workforce skill sets including preparing graduates with the right knowledge/experience, Industry 4.0 and self-driving smart laboratories.
Professor King Kuok (Mimi) Hii from Imperial College London presented work done at the UK’s first Grand Challenge Institute: the Centre of Rapid Online Analysis of Reactions (ROAR) and EPSRC Centre for Doctoral Training (CDT) in Next Generation Synthesis & Reaction Technology (rEaCt) where they champion education and skills training in automation and data-led chemical research.
Mimi delivered a very passionate talk about giving the younger generations the tools and knowledge and letting them explore, assembling the pieces themselves. It was fantastic to hear an esteemed academic talking about PhD students learning by playing. Letting people try things, fail, learn and then try again.
A Fast, Flexible and Fun Framework for Creating Automated Laboratories – FLab
Nicholas Jose from the University of Cambridge and Cambridge CARES in Singapore demonstrated how his start-up Accelerated Materials Ltd has been setting up smart labs using open-source automation, IoT devices and artificial intelligence. His demo of FLab showed how automating lab devices can not only be accessible to non-electrical engineers but also a great collaboration platform. I am not biased just because I like Python. The driver design part of things still seemed a bit elusive.
Nichlolas’ talk did open the floor for discussions around open source vs proprietary software when tools such as LabVIEW and MATLAB were brought into the equation. Within academia, open source feels like a clear path; after all, that’s how we give presentations and share ideas. However, is open source automation (free model) secure and reliable enough to ensure labs will function after an (un-paid) developer has left their labour of love unmaintained for years? Or do commercial entities value support, reliability, security and, most importantly, liability?
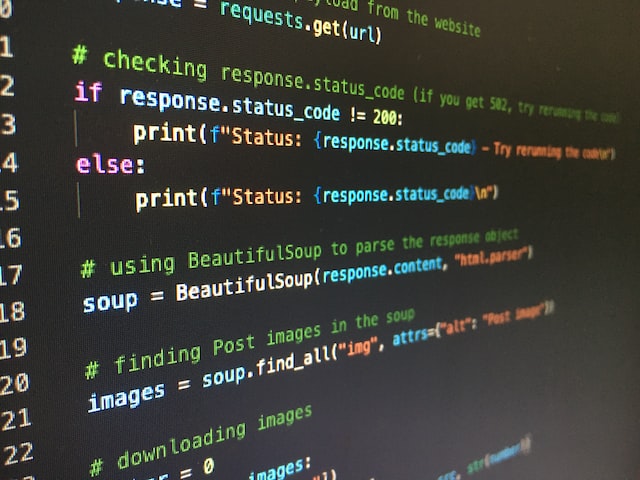
Taking Advantage of Digital Developments
Jon-Paul Sherlock, Head of Innovative Manufacturing Technology for AstraZeneca (AZ) delivered a presentation on how AZ plans to take advantage of digital developments in virtual experimentation, automation and digital twins. They have a very ambitious goal of launching 30 new medicines by 2030. It became very clear from the talk that AZ is not just focused on using digital tools for drug discovery (which is where we’ve seen more public engagement through AI systems like AlphaFold) but for the full development cycle, including manufacturing.
This is an exciting opportunity to further expand on our recent collaboration with AZ on the Digital Design Accelerator Platform (D-DAP), where the focus was placed on understanding the manufacturability of particles based on atomistic structure data. That project also served as an accelerant for developing the recent CSD-Particle toolkit.
Jason Williams, a principal scientist at the Research Center Pharmaceutical Engineering (RCPE) in Graz, Austria presented on the Digitization and Automation in the development of flow processes for API synthesis – a fantastic demonstration of continuous manufacturing combined with process analytical technology (PAT) and real-time chemometric processing.
It was interesting to see how they are using this platform to develop self-optimising processes, automated design of experiments (this would have been amazing in my PhD) and rapid process model building and predictive control. Such automation and model building would allow for much more precise experimentation, which would reduce timelines and make regulatory submission much easier.
A panel discussion concluded the morning session with the aforementioned speakers and Andrea Sauerwein from Johnson Matthey. The topics discussed were structured around what digital means in the context of R&D and manufacturing. Which of the new technologies were relevant and applicable to the current challenges? And how can these enable better processing chemistry and technology?
Much of the discussion was geared towards education and skill shortages within the workforce. A lot of the tools that seem to be fundamental to Industry 4.0 require a level of computational and programming literacy that is not currently up to standard, and whilst everyone wants to be part of the “revolution”, not everyone wants to learn the skill set. I believe “allergic to code” came up a couple of times during these discussions.
Structural Informatics Approaches to Transform Pharmaceutical Processes
After lunch, which was filled with discussions around ML and how to best apply it to non-solved problems, Andy Maloney from CCDC presented how structural informatics approaches can transform pharmaceutical processes. Andy covered the current approach we use at CCDC for carrying out “Health Checks” using solid form informatics to query the intermolecular bonding holding the crystal structure together and how we are now looking at Particle Informatics.
Using the new suite of CSD-Particle tools, Andy showed how it is possible to quantifiably describe the predicted chemical and roughness properties of a particle, enabling someone to go from molecule to particle properties using our suite of software. Not that I am biased in any way (I am part of the Particle Science Team at CCDC), but the discussion that proceeded was fantastic and showed real excitement in the field from both the computational and processing side of things.
Professor Joan Cordiner from the University of Sheffield discussed how digital tools have advanced for resolving operations and maintenance problems in reactions, separations and product properties. Joan mentioned a few stories from the ICI days, and whilst the tools have changed, some of the same old problems remain. Solvent selection and predictive maintenance in the digital age were the main points of conversation. Where does Machine Learning come to our aid, and how do we train the upcoming chemical engineers with the knowledge for Industry 4.0 whilst retaining the lessons learned by the experienced engineers retiring?
The final talk of the day was by Nessa Carson on how to automate your own HTE workflow. Whilst I no longer get to go into labs, Nessa’s talk about high throughput experimentation (HTE) was very engaging. Being “the coding person” in a research group who puts scripts together for people to save hours of their lives really resonated with me and my time as a PhD student.
My favourite part of Nessa’s talk was when she said, “People are scared of scripts and code; just call it an app. Give it a GUI with a single button”. This alone was revolutionary for me. I know it sounds simple, but as someone who regularly stares at code, it’s good to be reminded that not everyone cares about code. They want their problems solved; they don’t care what algorithm you use.
Learning from Examples Outside of Process Chemistry and Technology
The afternoon session concluded with a panel discussion where the topics included were: What can we learn from examples outside of process chemistry and technology? What skills will process chemists and technologists need for the digital future? The panellists were mostly in agreement that process chemistry is a little bit behind compared to other industries like aeronautics and mechanical design.
However, we are learning from their endeavours, and we have a slightly more squishy problem to solve. And back to the question of, is the labour force ready for Industry 4.0? Probably not right now, but we are getting there. The industry is pushing the right buttons and pulling the correct levers for people to train up with digital skills in mind.
Next Steps
Learn more about Solid Form Health Checks providing bespoke analysis of your crystal structure to assess risks and guide your development.
Learn more about CSD-Particle to anticipate manufacturing bottlenecks and guide formulation decisions with a deep understanding of particle behaviour.